江冠金1,陳翠仙2,張慶武1,張鵬霞1
(1.山東藍(lán)景膜技術(shù)工程有限公司,山東泰安271021;2.清華大學(xué),北京100084)
摘要:從乙醇的生產(chǎn)工藝出發(fā),以其中能耗最大的分離工藝為著眼點(diǎn),提出采用滲透氣化技術(shù)是解決能耗的有效途徑,列舉了國內(nèi)外在這方面研究和應(yīng)用的一些成果。
燃料乙醇是指對(duì)濃度為95%左右的食用乙醇或工業(yè)乙醇經(jīng)脫水、變性后,水體積小于0.5%的無水乙醇。燃料乙醇除具有替代車用燃料的功能外,還具有用作汽油辛烷值改進(jìn)劑和增加汽油氧含量以減少汽車尾氣中的CO、烴類污染的功能,同時(shí)還由于其來源于生物質(zhì),屬于可再生資源,被稱為“綠色能源”。對(duì)于緩解目前的能源短缺,減少空氣污染,調(diào)整我國農(nóng)村地區(qū)的產(chǎn)業(yè)結(jié)構(gòu)具有非常重大的現(xiàn)實(shí)意義。目前,我國政府已經(jīng)開始大力推動(dòng)燃料乙醇研究計(jì)劃,在河南、吉林和黑龍江等糧食主產(chǎn)區(qū)已經(jīng)有幾個(gè)大型燃料乙醇生產(chǎn)基地建成投產(chǎn)。在我國,燃料乙醇的生產(chǎn)方法跟國外相比還比較落后,生產(chǎn)成本高,燃料乙醇生產(chǎn)企業(yè)要大量依靠政府補(bǔ)貼,因此,探索新的生產(chǎn)方法,降低生產(chǎn)成本成為燃料乙醇生產(chǎn)中面臨的重要課題。
1燃料乙醇的生產(chǎn)工藝
乙醇的生產(chǎn)方法可概括為兩大類:發(fā)酵法和化學(xué)合成法?;瘜W(xué)法以化石原料為源頭,由于化石原料為不可再生資源,該方法的大規(guī)模應(yīng)用受到限制。我國乙醇生產(chǎn)以發(fā)酵法為主。按生產(chǎn)原料的不同,發(fā)酵法又分為淀粉質(zhì)原料生產(chǎn)乙醇、糖質(zhì)原料生產(chǎn)乙醇、纖維素原料生產(chǎn)乙醇以及用工廠廢液生產(chǎn)乙醇等。淀粉質(zhì)原料發(fā)酵法是我國生產(chǎn)酒精的主要方法。該法是以玉米、木薯等農(nóng)副產(chǎn)品為主要原料,對(duì)其中的淀粉成分進(jìn)行液化發(fā)酵制得。具體工藝流程如圖1所示。
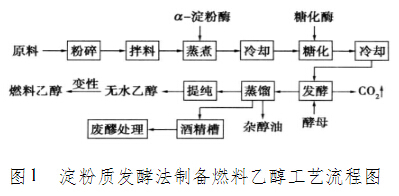
該工藝過程中的醇-水分離過程(包括蒸餾和提純過程)是整個(gè)生產(chǎn)過程中能耗最大的過程,不但決定了產(chǎn)品的產(chǎn)率和質(zhì)量,也直接影響到生產(chǎn)的成本。我國燃料乙醇價(jià)格之所以遠(yuǎn)遠(yuǎn)高于巴西等燃料乙醇生產(chǎn)大國,分離過程能耗過大、收率低及污染大是主要原因之一。
1.1母液蒸餾過程
經(jīng)酵母菌把糖轉(zhuǎn)變成酒精后,在成熟發(fā)酵母液內(nèi)除含有酒精和大量水分外,還含有固形物和許多雜質(zhì)。蒸餾就是經(jīng)過粗餾和精餾,取得合乎規(guī)格的酒精,同時(shí)得到副產(chǎn)物雜醇油,排出大量的酒糟。母液的蒸餾工段是能耗最大的工段,因此酒精生產(chǎn)降低能耗的關(guān)鍵就在于如何降低蒸餾段的能耗。除了調(diào)控好工藝本身的參數(shù),如控制好進(jìn)醪、供汽、冷卻水量,采用最佳回流比,采用最適塔板數(shù),合理增大板間距和汽速,運(yùn)用夾點(diǎn)技術(shù)進(jìn)行診斷調(diào)優(yōu)等,研究實(shí)踐表明:差壓蒸餾、熱泵蒸餾、熱耦合蒸餾等更能明顯降低蒸餾段的能耗,顯著降低生產(chǎn)成本。
1.2提純過程
蒸餾合格的酒精需要進(jìn)一步脫水并添加改性劑才能做燃料乙醇。脫水技術(shù)是生產(chǎn)燃料酒精的關(guān)鍵技術(shù)之一。發(fā)酵得到的酒精醪液經(jīng)普通精餾可得到接近乙醇-水恒沸濃度的酒精產(chǎn)品,其體積分?jǐn)?shù)為95.5%。而燃料乙醇要求酒精的體積分?jǐn)?shù)為99.8%,需用特殊脫水技術(shù)才能獲得合格產(chǎn)品。目前脫水技術(shù)分為傳統(tǒng)技術(shù)、改良傳統(tǒng)技術(shù)和非傳統(tǒng)技術(shù)3類:
傳統(tǒng)技術(shù)有真空蒸餾法和三元蒸餾法(或稱恒沸精餾法)。真空法對(duì)設(shè)備的要求高,運(yùn)行費(fèi)用昂貴;三元法引入的第三組分苯或環(huán)己烷等對(duì)人體有害,苯是一種公認(rèn)的致癌物,環(huán)己烷的毒性也受到人們的懷疑,并且該方法能耗高[7000~8000kJ/L(乙醇)]。
傳統(tǒng)改良技術(shù)即是在蒸餾段提到過的熱泵和差壓技術(shù),在恒沸精餾等傳統(tǒng)技術(shù)中應(yīng)用熱泵或差壓,兩者都可顯著提高蒸汽的利用率,達(dá)到節(jié)能的效果。非傳統(tǒng)技術(shù)主要包括超臨界和亞臨界提取技術(shù)、吸附脫水技術(shù)、超聲波與沸石吸附相結(jié)合技術(shù)、加鹽萃取技術(shù)及滲透氣化新技術(shù)等。
2滲透氣化膜技術(shù)在燃料乙醇分離工藝中的應(yīng)用現(xiàn)狀
滲透氣化技術(shù)是一種新的膜分離技術(shù),具有不需要引入第3組分,設(shè)備結(jié)構(gòu)簡單,單級(jí)分離效率高、無污染、耗能低等特點(diǎn)受到青睞。滲透氣化技術(shù)特別適用于有機(jī)物-水體系分離,不僅在傳統(tǒng)的大量有機(jī)物溶劑中脫除微量水領(lǐng)域(對(duì)應(yīng)采用透水膜)具有很大的優(yōu)勢(shì),在從大量水中抽提少量有機(jī)物溶劑領(lǐng)域(對(duì)應(yīng)采用透有機(jī)物膜)同樣顯示出很大的優(yōu)越性,因此特別適合應(yīng)用于燃料乙醇的制備,可以直接將乙醇發(fā)酵母液處理得到無水級(jí)的乙醇,是未來燃料乙醇生產(chǎn)的發(fā)展方向。圍繞著滲透氣化技術(shù)如何應(yīng)用于燃料(無水)乙醇的生產(chǎn),國內(nèi)外學(xué)者都做了大量的工作,獲得了很多的寶貴經(jīng)驗(yàn)。尤其是國內(nèi)的研究者,緊追國際上的同行,在科研條件較差的條件下,仍然取得了很大的成績,取得了比較多的成功案例。
2.1滲透氣化透水膜技術(shù)
滲透氣化透水膜是最早實(shí)現(xiàn)工業(yè)應(yīng)用的滲透氣化膜。1982年,德國GFT公司率先成功地把滲透氣化技術(shù)應(yīng)用到無水乙醇的生產(chǎn)中,在巴西建成了產(chǎn)能為1300L/d的無水乙醇工廠。在隨后的幾年中,GFT公司在西歐和美國建立了20多個(gè)規(guī)模更大的裝置(1500~2000L/d)。Lurge公司應(yīng)用GFT膜在德國Karlsruhe附近的一個(gè)造紙廠建立了1套生產(chǎn)能力為6000~12000L/d的乙醇脫水制無水乙醇的裝置。1988年,由GFT公司設(shè)計(jì),在法國Betheniville建成世界上第1個(gè)最大的滲透氣化法脫水制無水乙醇的工廠,其生產(chǎn)能力為150000L/d無水乙醇,料液為94%的乙醇水溶液,產(chǎn)品含水質(zhì)量濃度小于2000mg/L。
我國在這方面的研究起步稍晚,但是也取得了較為豐碩的成果。浙江大學(xué)、中國科學(xué)院以及清華大學(xué)等科研院校率先開展了這方面的研究,此后眾多的院校、科研機(jī)構(gòu)和公司都參與到滲透氣化技術(shù)的研究與應(yīng)用中來。其中清華大學(xué)從20世紀(jì)80年代即開始滲透氣化技術(shù)的研究,先后承擔(dān)了國家“973”、“863”相關(guān)項(xiàng)目的攻關(guān)工作,取得了多項(xiàng)技術(shù)成果。從2001年開始,清華大學(xué)與山東藍(lán)景膜技術(shù)工程有限公司合作,共同開展?jié)B透氣化技術(shù)的產(chǎn)業(yè)化工作,先后建成了十多套滲透氣化有機(jī)溶劑脫水裝置。短短幾年,采用山東藍(lán)景膜技術(shù)工程有限公司的滲透氣化膜技術(shù)進(jìn)行脫水的裝置年總處理量已經(jīng)超過了4萬t/a,占到了國內(nèi)滲透氣化市場90%以上的份額,其中乙醇的總處理量超過2萬t/a。
2.2滲透氣化透醇膜技術(shù)
滲透氣化透醇膜技術(shù)生產(chǎn)乙醇目前還停留在實(shí)驗(yàn)室階段,還沒有完全實(shí)現(xiàn)產(chǎn)業(yè)化。但經(jīng)過眾多的科研人員的研究,已經(jīng)看到了產(chǎn)業(yè)化的曙光。Li等采用濕處理法制備了PDMS/CA復(fù)合膜,發(fā)現(xiàn)其性能有很大的提高,在40℃時(shí),乙醇含量5%的水溶液中通量和分離因子分別達(dá)到1300g/(m2·h)和8.3。沸石分子篩具有特殊的孔道結(jié)構(gòu),且比表面積大,吸附能力強(qiáng),因而具有很好的分離性能,被應(yīng)用于有機(jī)物分離體系中。Lin等以莫來石為支撐體原位合成16h后,所得的沸石分子篩膜的通量為0.93kg/(m2·h),分離因子為106,是目前研究報(bào)道中性能最優(yōu)異的透醇膜,已經(jīng)接近工業(yè)化必需的條件。
一旦透醇膜實(shí)現(xiàn)了產(chǎn)業(yè)化,即可以實(shí)現(xiàn)發(fā)酵-滲透氣化分離的耦合,從而可以省去能耗最大的蒸餾步驟(或者大大減少蒸餾的處理量)。發(fā)酵-滲透氣化分離的耦合工藝具有如下優(yōu)勢(shì):
(1)可從發(fā)酵液中原位分離乙醇,使之維持在一個(gè)相對(duì)恒定的濃度,使乙醇對(duì)酵母細(xì)胞的抑制作用保持低水平甚至消除,從而維持反應(yīng)器中適當(dāng)?shù)慕湍讣?xì)胞濃度和高生物活性,實(shí)現(xiàn)高密度發(fā)酵和較高的原料糖轉(zhuǎn)化率。
(2)可直接冷凝分餾得到較高濃度的乙醇,降低乙醇生產(chǎn)能耗。滲透氣化膜技術(shù)的能耗僅為傳統(tǒng)蒸餾法的1/10~1/3,且無“三廢”產(chǎn)生,避免了環(huán)境污染,同時(shí)可省去傳統(tǒng)蒸餾法的廢水處理工藝。
(3)可實(shí)現(xiàn)連續(xù)發(fā)酵,使反應(yīng)器的容積顯著減小,以達(dá)到更大的生產(chǎn)規(guī)模,并易于實(shí)現(xiàn)過程的自動(dòng)化控制,保證工藝穩(wěn)定運(yùn)行。
(4)進(jìn)料可采用高濃度的糖,減少發(fā)酵過程的用水量,進(jìn)一步降低能耗。
3展望
隨著石油資源的日益枯竭,作為可循環(huán)利用的燃料乙醇必然會(huì)在將來獲得巨大的發(fā)展。而滲透氣化技術(shù)作為一種新興的分離技術(shù),其特點(diǎn)正好切合燃料乙醇生產(chǎn)的要求,必定會(huì)擁有廣闊的前景。 |